以某燃煤电厂烟气脱硫(FGD)系统为例,分析了传统FGD废水系统存在设计缺陷、设备故障率高等问题。通过多项优化和技术改造,降低了废水中的固体含量,确保了系统正常运行,降低了运行维护成本。并提出了切实可行的解决方案和建议,为未来实现废水零排放奠定了坚实的基础。
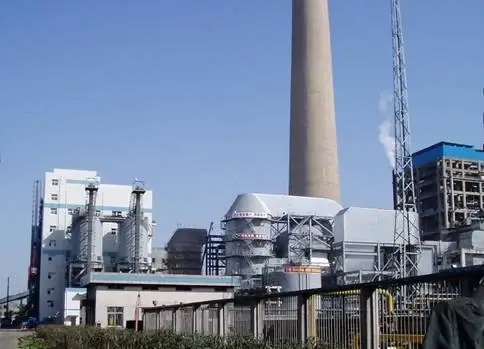
1.系统概述
燃煤电厂普遍采用石灰石-石膏湿法烟气脱硫工艺,以石灰石(CaCO₃)作为吸收剂。该工艺不可避免地会产生烟气脱硫废水。本案例中,两套湿法烟气脱硫系统共用一套废水处理装置。废水来源为石膏旋流器溢流,采用传统方法(三罐系统)处理,设计处理能力为22.8吨/小时。处理后的废水经泵送至6公里外的处置场进行抑尘处理。
二、原有制度存在的主要问题
加药泵的隔膜经常发生泄漏或故障,导致无法连续加药。板框压滤机和污泥泵的高故障率增加了劳动力需求,阻碍了污泥的清除,减缓了澄清器的沉淀速度。
废水源自石膏旋流器溢流,密度约为1,040 kg/m³,固体含量为3.7%。这影响了系统连续排放处理水和控制吸收塔内有害离子浓度的能力。
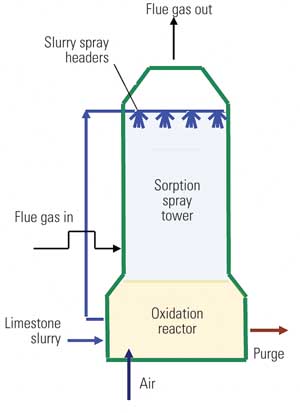
3. 初步修改
改善化学药剂投加:
在三罐系统顶部安装了额外的化学罐,以确保通过重力进行一致的剂量,由在线浓度计.
结果:水质有所改善,但仍需进行沉淀。日排放量降至200立方米,不足以保证两套烟气脱硫系统稳定运行。投加成本较高,平均每吨12元。
废水再利用用于抑尘:
在澄清器底部安装了泵,将部分废水重新引导至现场灰仓进行混合和加湿。
后果:虽然降低了处置场的压力,但浊度仍然较高,不符合排放标准。
四、当前优化措施
随着环境法规越来越严格,进一步的系统优化是必要的。
4.1 化学调节与连续操作
通过增加化学剂量将pH值维持在9-10之间:
日用量:石灰45公斤、混凝剂75公斤、絮凝剂。
确保系统间歇运行后每天排放240立方米清水。
4.2 应急泥浆罐的改造
应急罐的双重用途:
停机期间:泥浆储存。
运行中:自然沉淀,提取清水。
优化:
在各个油箱层增加阀门和管道,以实现灵活操作。
沉淀的石膏返回系统进行脱水或再利用。
4.3 系统范围的修改
通过将真空带式脱水系统的滤液重新引导至废水缓冲罐,降低进入废水中的固体浓度。
通过在应急池中添加化学药剂来缩短自然沉降时间,从而提高沉降效率。
5.优化的好处
提高容量:
连续运行,日排放达标废水400多立方米。
有效控制吸收器中的离子浓度。
简化操作:
不再需要板框压滤机。
减少污泥处理的劳动力。
增强的系统可靠性:
废水处理计划更加灵活。
设备可靠性更高。
节省成本:
化学品使用量减少为石灰(1.4 kg/t)、混凝剂(0.1 kg/t)和絮凝剂(0.23 kg/t)。
处理成本降至5.4元/吨。
每年节省化学品成本约948,000元人民币。
结论
烟气脱硫废水系统的优化显著提高了效率,降低了成本,并符合了更严格的环保标准。这些措施为类似系统实现废水零排放和长期可持续发展提供了参考。
发布时间:2025年1月21日